Het gebruik van enkelvoudig gevulkaniseerd PU-zink
Inleiding
Het marktaandeel van vochtuithardende urethanen voor verfprojecten neemt geleidelijk toe vanwege hun langdurige corrosiebescherming, weerstand tegen chemicaliën en graffiti, superieur glansbehoud en kleuruitstraling. Daar komt nog bij dat vochtuithardende urethanen kosten- en tijdbesparend zijn door hun oppervlaktetolerantie, snelle droging, gebruiksvriendelijkheid en het feit dat zij onder slechte weersomstandigheden kunnen worden aangebracht.
De technologie werd oorspronkelijk uitgevonden door Bayer Material Science (nu Covestro) uit Duitsland. Het meest opvallende verschil met epoxy coatings is dat, in plaats van twee componenten samen te voegen, het uithardingsproces in gang wordt gezet door de reactie van het polyurethaan bindmiddelsysteem met atmosferisch vocht. Dit is de reden waarom vochtverhardende urethanen kunnen worden aangebracht tot 98% relatieve vochtigheid. Oppervlaktevocht voltooit in feite de chemische reactie, waardoor deze coatings een uitstekende hechting vertonen op zichtbaar vochtige oppervlakken. In de poriën en haarvaten van het staal, waar gewoonlijk vocht aanwezig is, dringt de coating diep door om sterke chemische bindingen te vormen. Aangezien het vocht in dit proces wordt verbruikt, is er een sterk verminderd risico van blaasjes door water dat onder de verflaag zit.
Productiviteits- en prestatievoordelen
In een tijd waarin de levenscycluskosten van een constructie meer en meer worden berekend over een langere periode, soms zelfs tot 50 jaar, wordt het steeds belangrijker een corrosiebeschermingsoplossing te bieden die een lang interval tot het eerste onderhoud mogelijk maakt.
Met de vandaag beschikbare instrumenten voor activabeheer is het mogelijk de werkelijke onderhoudskosten af te zetten tegen de geraamde onderhoudskosten voor de levenscyclus. Afwijkingen door bijvoorbeeld voortijdige verfdefecten kunnen gemakkelijk worden gecontroleerd en de financiële gevolgen kunnen nauwkeurig worden gekwantificeerd. Deze trend is wellicht een van de belangrijkste redenen waarom bedrijven afstappen van het kortetermijndenken tijdens de bouw- of grote onderhoudsfase van een project. Meer en meer wordt de voorkeur gegeven aan langdurige corrosiebescherming, ook al leidt dit tot een verhoging van de totale projectkosten. De verfgerelateerde kosten vormen in het algemeen echter slechts een klein percentage van de totale projectkosten. Als de looptijd van een nieuwbouw- of M&R-project kan worden verkort en de tijd tot het eerste onderhoud kan worden verlengd door een geschikt coatingsysteem te kiezen, wegen de financiële voordelen ruimschoots op tegen de extra verfgerelateerde kosten.
Vochtverhardende polyurethanen bieden langdurige corrosiebescherming voor staalconstructies in de meest veeleisende omgevingen.
Bovendien bieden zij ook een aantal praktische voordelen bij zowel nieuwbouw als onderhoud. Een van de grote voordelen is dat deze coatings kunnen worden aangebracht op stalen substraten met minimale/verminderde voorbereiding van het oppervlak, zoals elektrisch reinigen ST3, UHP Waterjetting WJ 2 – 3 L, gritstralen SA1.5 – SA2. Andere voordelen van vochtverhardende polyurethanen zijn dat zij kunnen worden aangebracht tot 98% relatieve vochtigheid, uitharden tot min 5 graden Celsius zonder toevoegingen, permanent flexibel zijn, zeer slijt- en slagvast zijn en over de meeste bestaande verfsoorten kunnen worden aangebracht.
Steelpaint GmbH
Steelpaint is een Duitse fabrikant van coatings, gespecialiseerd in vochtuithardende polyurethanen, die al meer dan 30 jaar actief is.
Onze belangrijkste markten zijn bruggen, hydraulische staalconstructies (buis- en damplanken, aanlegsteigers, sluizen, stormvloedkeringen enz.), marine (laadruimen van bulkschepen, ballasttanks), offshore (platforms, booreilanden, aken), industrie (pijpleidingen, opslagtanks).
Corrosiebescherming in laadruimen aan boord van bulkschepen
De aard van de door bulkers vervoerde ladingen maakt inspectie van bulkcarriers op kritieke plaatsen verplicht, vooral wanneer in de romp staalplaten met hoge treksterkte zijn gebruikt. De rompen worden tijdens het laden en lossen van de lading blootgesteld aan buigspanning in de lengterichting en schuifkrachten.
Bulkschepen zijn groter geworden en vervoeren steeds meer verschillende ladingen. Zij zijn wettelijk verplicht om de romp jaarlijks te laten inspecteren.
Tijdens het laden en lossen van de lading kan structurele schade aan de romp ontstaan.
Tegenwoordig zijn moderne bulkers ontworpen om ijzererts, bauxiet, fosfaten, steenkool en graan te vervoeren. Bulkers maken bijna 40% van de wereldvloot uit.
Er zijn een aantal methoden om te laden:
Moderne kranen kunnen 1000-2000 ton/uur laden. Transportsystemen kunnen tussen 100 en 700 ton/uur laden, waarbij de moderne systemen tot 16000 ton/uur in staat zijn. Stel je de spanningen voor die bij deze snelheden op de romp worden uitgeoefend!
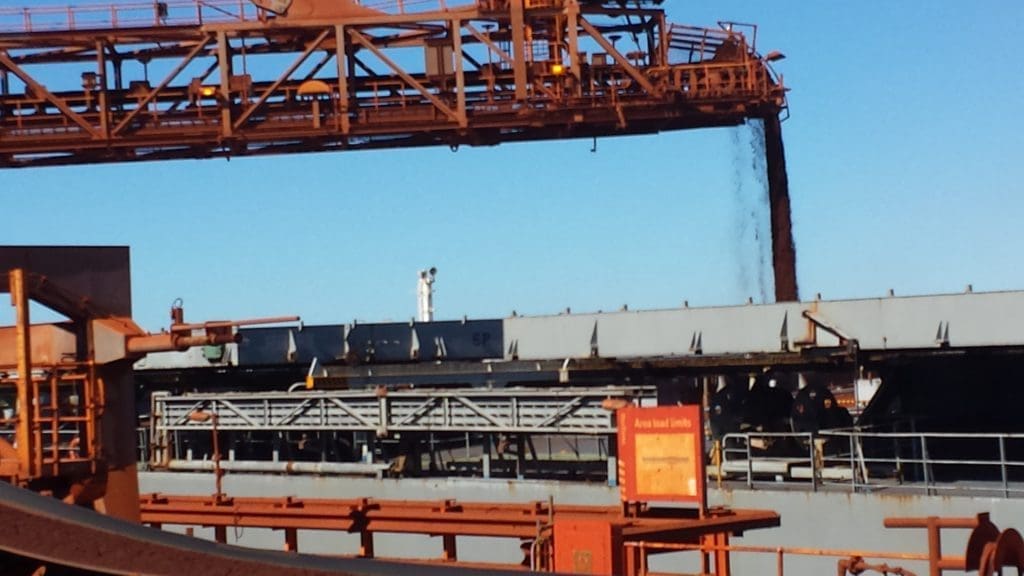
Lossen:
Afhankelijk van de lading worden gewoonlijk kranen gebruikt en de lossingssnelheid hangt af van de grootte van de bak/grijper en de capaciteit van de kraan, die gemiddeld ongeveer 800 ton/uur bedraagt.
Zodra het grootste deel van de lading is gelost, worden voorladers en bulldozers in de ruimen neergelaten om het residu in grote hopen te leiden die door de kraanbakken worden verzameld, waarna de ruimen met de hand worden uitgeborsteld.
De meest kritieke plaatsen in de laadruimen zijn de onderste trechter- en bodemplaten. Hier is de impact van de bulldozer en de grijper het meest extreem. De bodemplaten worden gewoonlijk niet geschilderd omdat er geen andere coatingsystemen bestaan die bestand zijn tegen de extreme impact.
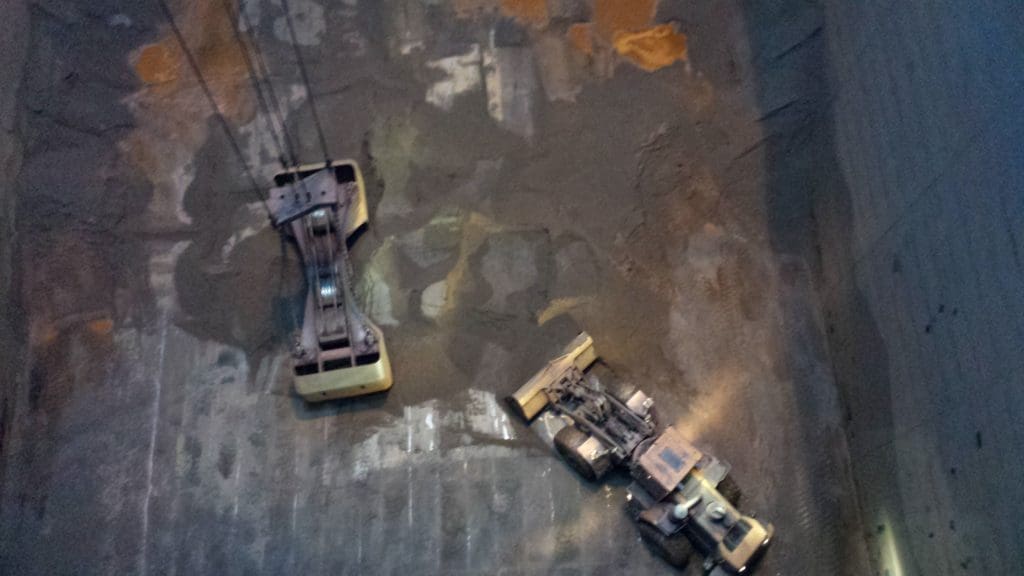
Test
In 2008 werd Steelpaint uitgenodigd om deel te nemen aan een test op ware grootte aan boord van M/V Sophie Oldendorff, een Panamax bulkschip dat zeer schurende ladingen zoals ijzererts, steenkool enz. vervoert en eigendom is van Oldendorff Carriers GmbH.
Het doel van de test was het meest slijt- en slagvaste coatingsysteem voor de laadruimen te vinden. In elk ruim werd een ander coatingsysteem aangebracht om de prestaties van elk coatingsysteem onder exact dezelfde omstandigheden te kunnen vergelijken.
Steelpaint werd benoemd tot ruim nr. 3, dat op dit type schip ook wordt gebruikt als ballastruimte tijdens de lege vaart. De blootstelling aan slijtage en mechanische impact in combinatie met zeewater maakt deze greep tot de grootste uitdaging voor de prestaties van een coatingsysteem.
Het toegepaste coatingsysteem was 2 x 100 micron PU-Zink. De andere ruimen werden bekleed met versterkte epoxy coatings met een droge laagdikte variërend van 600 tot 1200 micron.
Voordelen PU-Zink
PU-Zink heeft een aantal principiële kenmerken die het tot een superieure coating voor dit specifieke doel maken:
- Het heeft een uitstekende hechting aan het stalen substraat
- Er zit 93% zink in de droge laag die zorgt voor kathodische bescherming. Als er een beschadiging is zal het omringende zink zich opofferen in plaats van het staal. Zo wordt corrosie voorkomen
- Het blijft flexibel en buigt daarom mee met het staal wanneer het wordt beschadigd door de grijper of bulldozer.
- Het kan in meerdere lagen worden aangebracht zodat een dikke laag zink op het staal kan worden aangebracht.
- Het is oppervlakte-tolerant en kan door de bemanning worden onderhouden tot de volgende droogdok.
Testresultaten
Na 6 maanden werden alle ruimen geïnspecteerd en werden de prestaties van de verschillende coatingsystemen geëvalueerd. Het bleek dat alleen ruim 3 in uitstekende staat was. De coatingsystemen in alle andere ruimen vertoonden de gebruikelijke tekenen van afbraak en corrosie.
Tijdens de volgende onderhoudsdroogdok, 2,5 jaar na de proefvaart, werd een eindevaluatie uitgevoerd. Het bleek dat ruim 3 minder dan 5 procent van het totale oppervlak was afgebroken. De gecorrodeerde plekken werden gerepareerd door reiniging met een powertool ST3 en bijgewerkt met twee lagen PU-Zink. De reparaties werden uitgevoerd vanuit een mand, geen steigers nodig.
De coatings in de andere ruimen waren voor 50-70% afgebroken en vereisten steigers, bijna een volledige ontploffing en volledig opnieuw schilderen. Het verschil in reparatiekosten met ruim 3 was enorm en vanaf dat moment heeft de eigenaar geleidelijk de laadruimen van zijn eigen vloot vervangen door PU-Zinc.
Nieuwbouw
Toen Oldendorff Carriers in 2013 een uitgebreid nieuwbouwprogramma lanceerde, werd het PU-Zinc systeem overwogen als mogelijkheid voor de laadruimen van de nieuwe schepen. Om dit besluit te rechtvaardigen werd een inspectie uitgevoerd aan boord van M/V “E. Oldendorff” een Panamax zelflosser.
Hier was de PU-Zinc 1,5 jaar in gebruik. Dit schip was in gebruik als overlaadstation in de Perzische Golf. De laad- en losoperaties gingen praktisch continu door, wat ook betekende dat het PU-zink aan maximale schokken en slijtage werd blootgesteld.
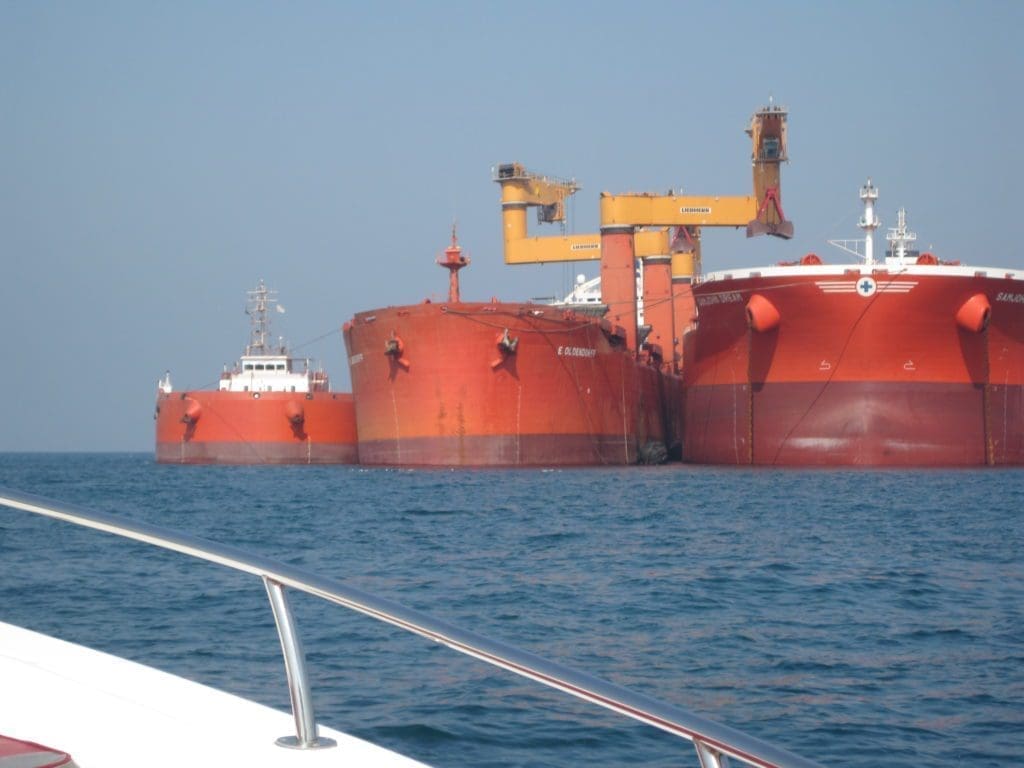
M/V “E. Oldendorff” in het midden afgebeeld
Inspectie:
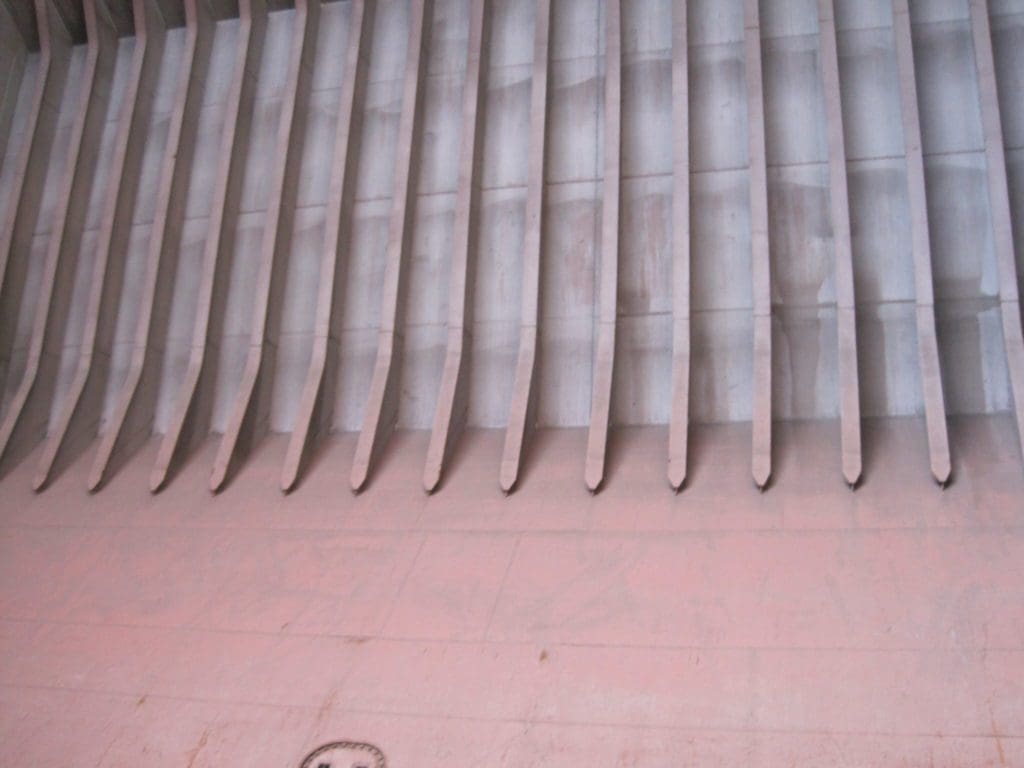
Totaalbeeld laadruimte na 1,5 jaar overladen ijzererts
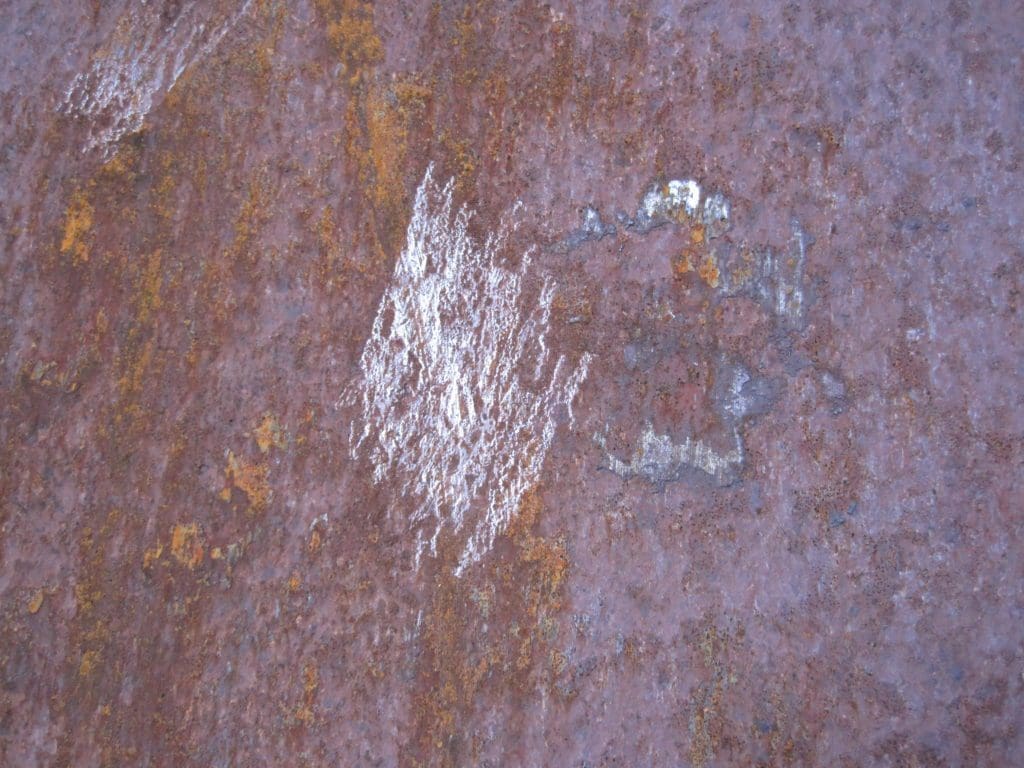
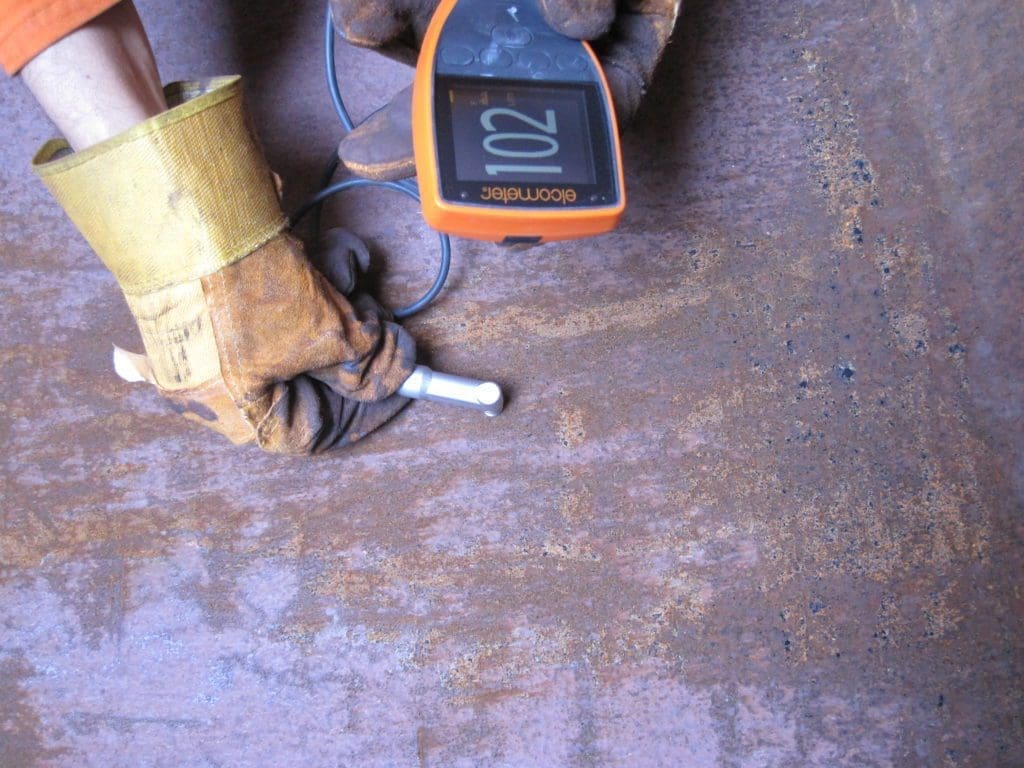
De beschadigde delen op de onderste trechterplaten leken op het eerste gezicht te corroderen. De roestvlekken waren echter gewoon ijzerertsresten die zich op de PU-Zink hadden afgezet. Na verwijdering met draadborstel of schraper verscheen onmiddellijk de metaalachtige werking van de PU-Zink. Metingen met een droge laagdiktemeter toonden aan dat op alle beschadigde plaatsen voldoende zink overbleef om voldoende corrosiebescherming te bieden.
In feite bleek uit de inspectie dat er na 1,5 jaar dienst nul procent corrosie was in het ruim dat werd geïnspecteerd.
Na deze succesvolle inspectie kreeg Steelpaint de levering van PU-Zink voor alle laadruimen van 11 nieuwbouwschepen in China.
9 x 39000 DWT bij Nanjing Jinling
2 x 94000 DWT bij Nieuw Yangzijiang
Proeven op bodemplaten
Testgebied:
Op basis van de uitstekende resultaten op de onderste hopperplaten zijn wij een testprogramma gestart aan boord van de M/V “Berge Bureya”, een VLOC van Bergebulk. Het doel van deze proef was na te gaan of PU-Zink ook op de bodemplaten bevredigende prestaties zou leveren.
Er werden twee oppervlakten van in totaal 100 m2 toegepast. Eén in het midden van het ruim, waar de impact van de grijper en de bulldozer het grootst is, en één gedeeltelijk op de bovenkant en de onderste trechter.
De oppervlaktevoorbereiding was slurryblast SA2 en het coatingsysteem 2 x 100 micron PU-Zink en op een derde van het oppervlak werd 3 x 100 micron PU-Zink aangebracht. Alle werkzaamheden werden uitgevoerd door een rijdende bemanning tijdens een lege tocht van het schip naar Tubaro in Brazilië. Het schip had een vast handelspatroon tussen Tubaro (laden) en Rotterdam (lossen). Dit maakte het gemakkelijker om de resultaten van de test te controleren.
De resultaten na de eerste twee runs zagen er veelbelovend uit. Wij zagen dat er zelfs bij de zwaarste beschadigingen nog voldoende zink op het oppervlak zat om voldoende corrosiebescherming te bieden. Op de paar plaatsen waar de PU-Zink bijna helemaal weg was, verhinderde het omringende zink dat het staal corrodeerde.
Test op volle schaal:
Na de bevredigende testresultaten aan boord van M/V “Berge Bureya” werd besloten tot een volledige toepassing, in de vorm van een grootschalige test in alle 9 ruimen aan boord van de Capesize bulker M/V “Berge Matterhorn”. Tijdens het droogdok in Shenzen China werd de PU-Zink aangebracht op de bodemplaten en onderste trechters tot ongeveer 1,5 mtr. Oppervlaktevoorbereiding gritstralen SA2, coatingsysteem 2 x 100 micron PU-Zink.
Inspectie:
Na 15 maanden werden de laadruimen geïnspecteerd in Krishnapatnam India.
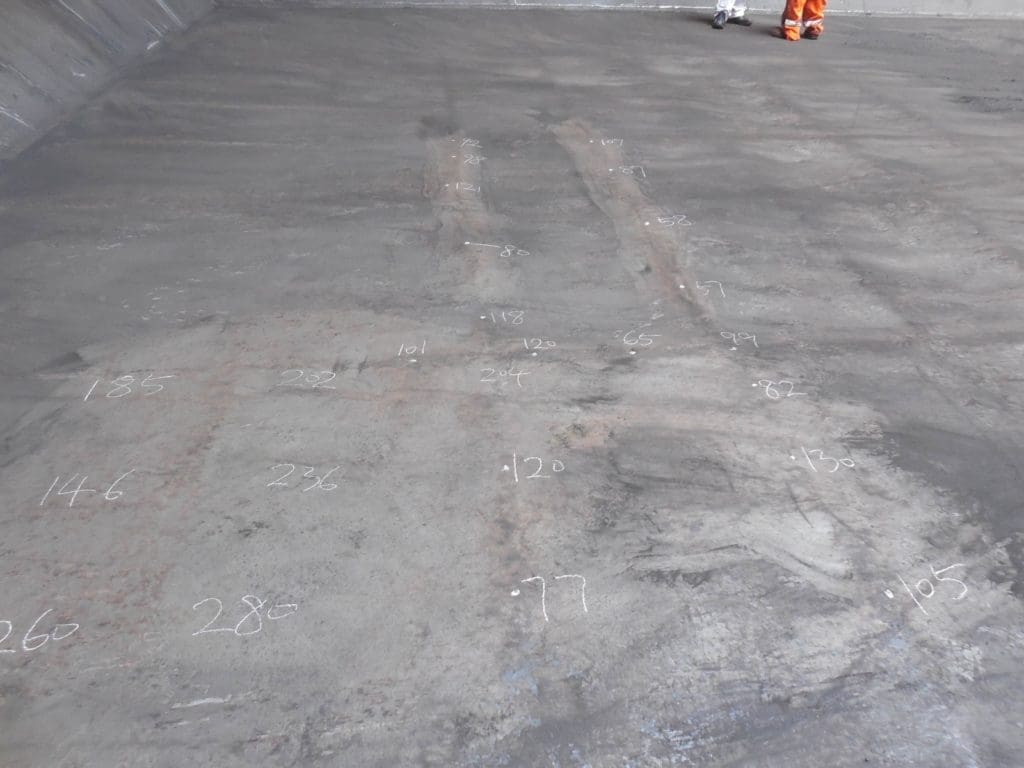
De resultaten waren zeer goed. Er is geen corrosie gevonden. Op 80% van het oppervlak was de dikte van het PU-zink volledig intact, er was geen onderhoud nodig. In 7% van het gebied was de droge laagdikte van de PU-Zink afgenomen tot 100 micron, geen onderhoud nodig. In 3% van het gebied was de droge laagdikte teruggebracht tot 50 micron; op dit punt was geen onderhoud nodig. Bovenop de dubbele bodemframes wordt de coating meer geschuurd dan op andere plaatsen omdat deze gebieden hoger liggen en dus meer blootgesteld zijn aan de impact van de bulldozer. In totaal maakt dit gebied 10% van de totale oppervlakte uit. Op veel plaatsen bovenop de frames was de dikte verminderd tot onder de 50 micron. Hier wordt aanbevolen de dikte van het zink terug te brengen tot de oorspronkelijk gespecificeerde dikte.
Onderhoud
Voor deze gebieden werd een onderhoudsplan ontwikkeld voor de bemanning. De onderhoudswerkzaamheden kunnen tijdens lege ritten met eenvoudig gereedschap worden uitgevoerd. De enige vereiste voorbereiding van het oppervlak is hogedrukreiniging met water om alle ladingresten goed te verwijderen en licht schuren van de frames met een staalborstel of schijf. Daarna kan de PU-Zinc worden aangebracht met een spuit- of rolprocédé, waarbij 2 tot 3 lagen moeten worden aangebracht.
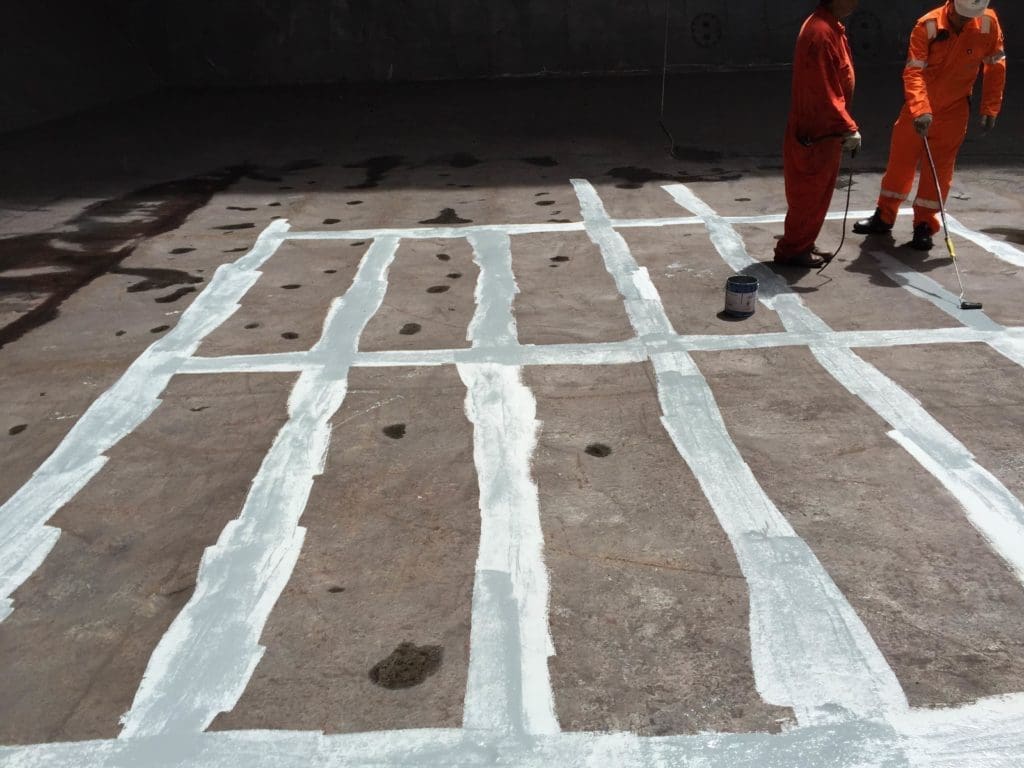
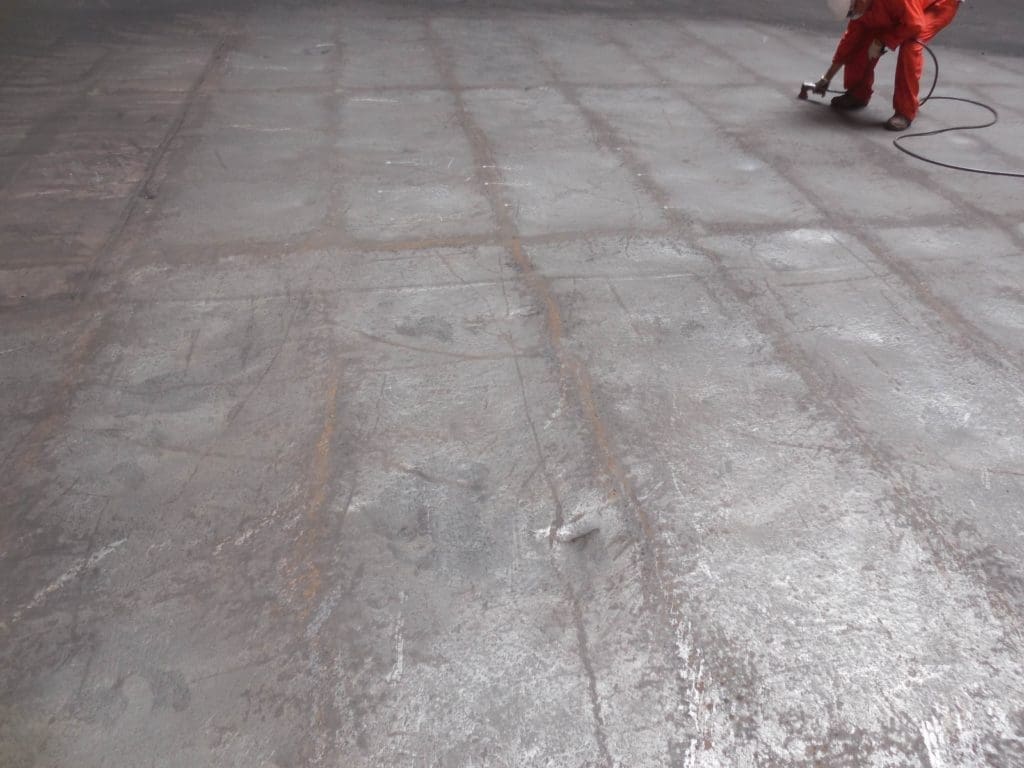
Op deze manier kan het coatingsysteem tot de volgende droogdok behouden blijven, wordt corrosie voorkomen en wordt het verlies aan staaldikte op een zeer kosteneffectieve manier onder controle gehouden.